NEWS
OPTIMAL PALLET WAREHOUSE PLANNING: SYSTEMS, STRATEGIES AND COMMON MISTAKES.
An efficient pallet warehouse needs to do more than just store pallets. It requires thoughtful planning, precise dimensioning and optimal alignment with the material flow. In this article, you’ll learn how to plan your pallet warehouse, what pallet storage systems and strategies can help you optimize your processes, and how to avoid common mistakes.
WHAT IS A PALLET WAREHOUSE?
A pallet warehouse is a storage structure specifically designed for storing pallets. These may include Euro pallets (1,200 x 800 mm), industrial pallets (1,200 x 1,000 mm), custom formats or mesh box pallets. Pallets can be stacked on the floor (block storage), placed in racking systems or managed and moved using automated systems.
Depending on the industry, storage volume, product variety, and turnover frequency, different storage types and technologies are used. However, they all share one thing: they must make the most of the available space while ensuring accessibility and process efficiency.
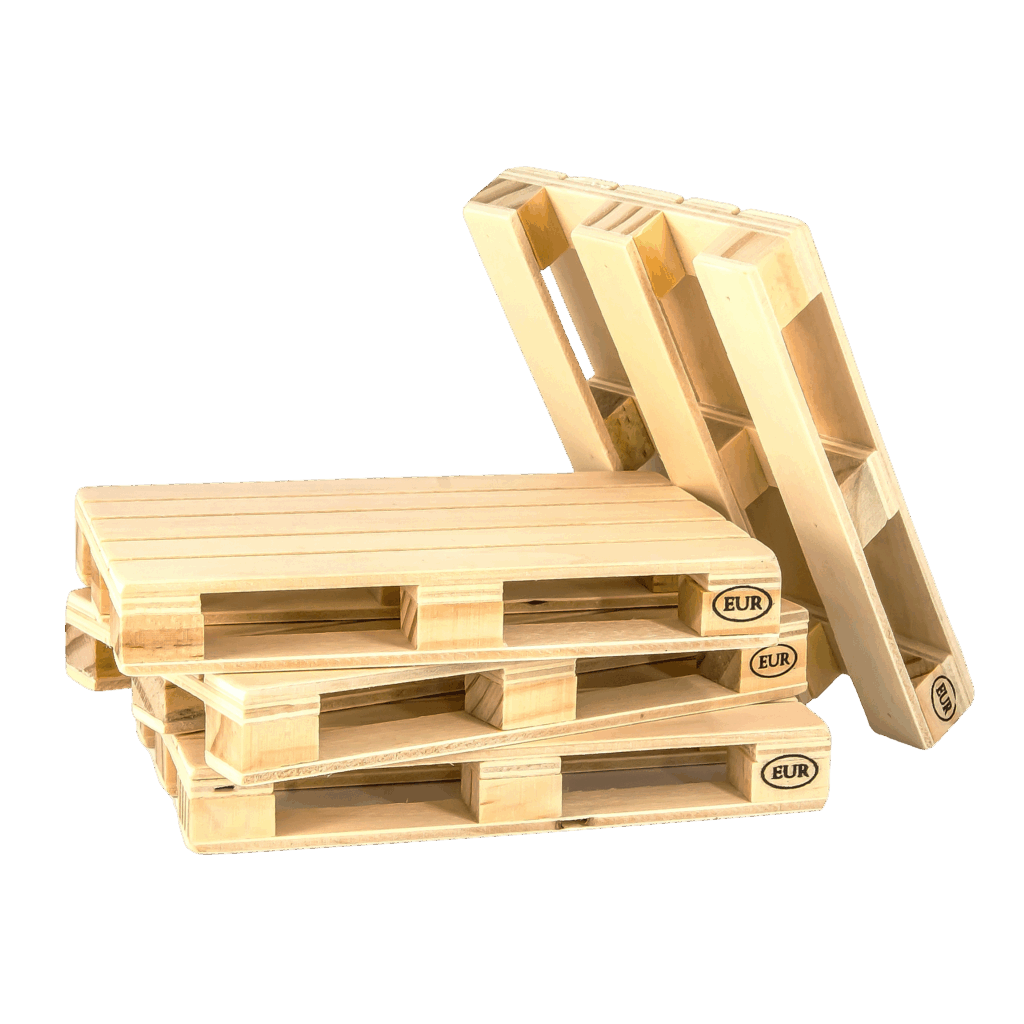
HOW CAN PALLETS BE STORED?
→ BLOCK STORAGE.
The simplest and oldest method: block storage. Here, pallets are stacked directly on the floor. This works especially well when storing large quantities of a single item. The storage density is high, but access is limited. LIFO (Last In, First Out) is usually the standard.
→ HIGH-BAY WAREHOUSE.
A high-bay warehouse makes use of the building’s height to store pallets on multiple levels, saving space. These systems are operated by stacker cranes (SRMs), shuttles, or forklifts. This storage type is ideal for companies with high inventory turnover. Narrow-aisle systems with automated technology offer high space efficiency and reduce traffic areas.
→ FLOW AND PUSH-BACK RACKS.
These systems rely on inclined roller conveyors. In flow racks, pallets are loaded on one side and retrieved from the other – perfect for a clean FIFO principle. Push-back racks work with a reverse rolling mechanism, supporting a LIFO strategy with high space efficiency.
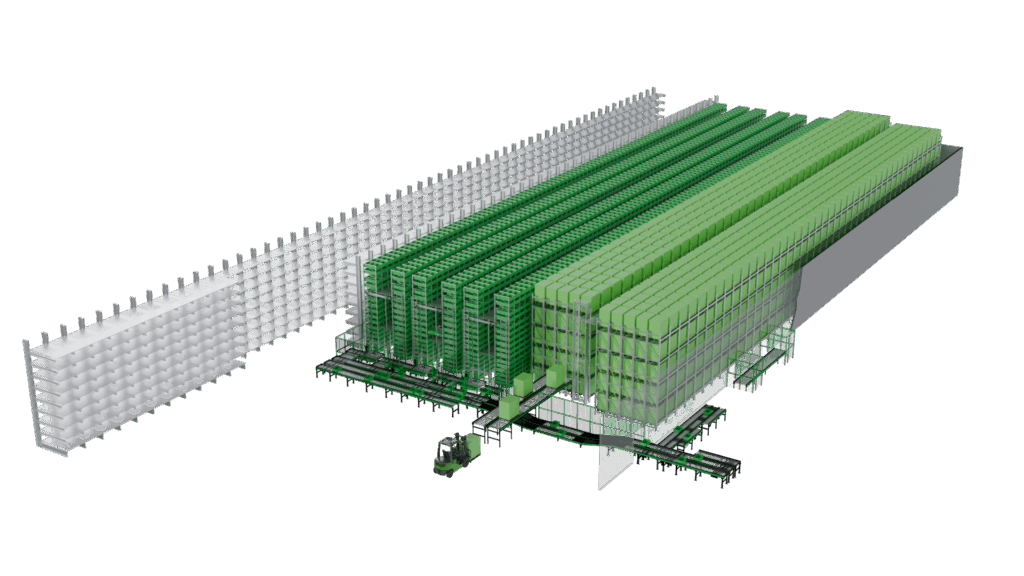
1.902 storage locations for Euro pallets and mesh box pallets.
6 MOVU pallet shuttles
Technical Data:
- Max. load: 1500 kg
- Max. speed: 1.4 m/s
- Max. acceleration: 0.5 m/s²
Pallets/mesh boxes are removed from the conveyor line using forklifts.
HOW MANY PALLETS FIT IN A WAREHOUSE?
The capacity of a pallet warehouse depends on several factors, including the type of storage, available space and pallet size.
In this Fb customer project, Euro pallets (max. 1,000 kg) and mesh box pallets (max. 1,000 kg) are stored. There are 1.902 storage locations, with pallets stored 5–6 deep in the racking system.
MESH BOXES AS AN EFFICIENT ADDITION TO PALLET WAREHOUSES.
Alongside classic pallets, mesh boxes play a key role in modern pallet warehouses. These robust steel containers are ideal for loose, bulky or sensitive goods. Thanks to standardized dimensions, they integrate easily into existing racking systems and can be moved with industrial trucks. Their stackability and open design allow for efficient storage processes and easy content inspection.
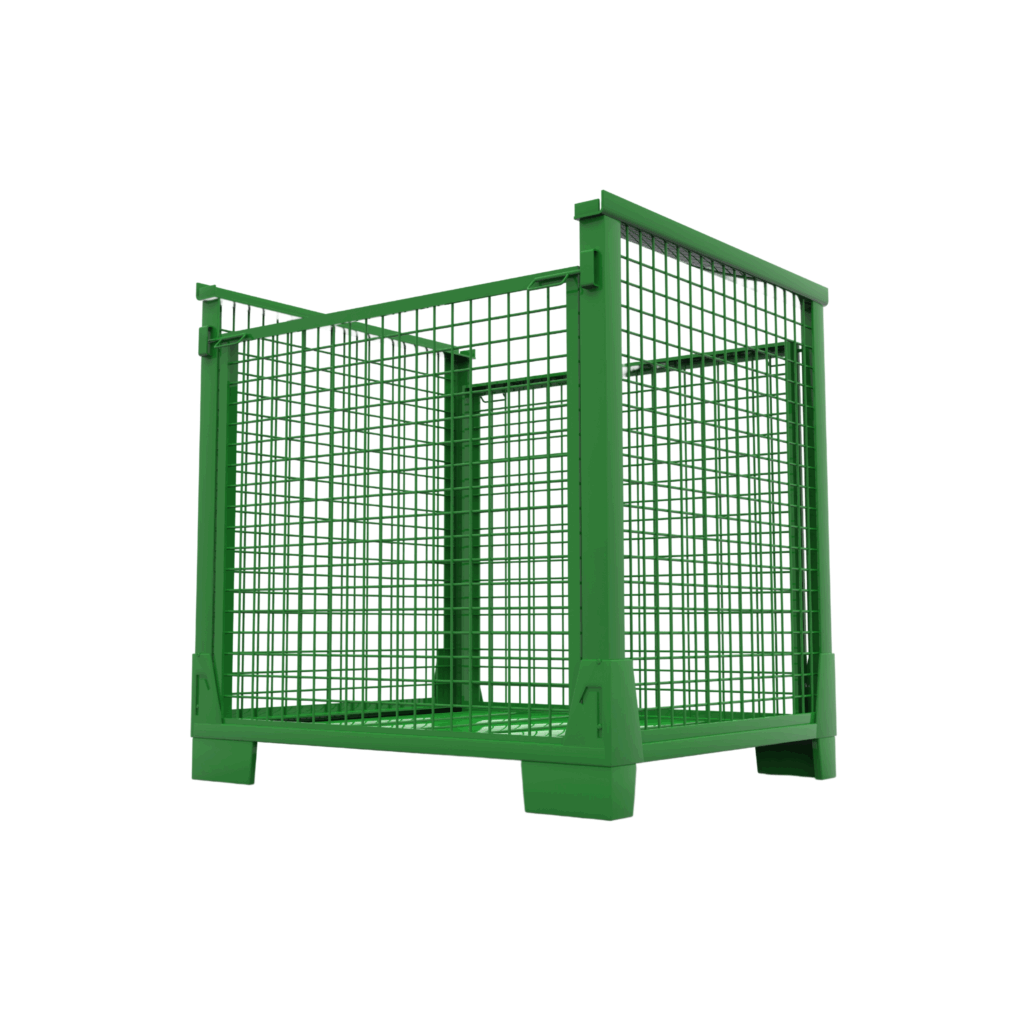
PLANNING A PALLET WAREHOUSE.
Successful pallet warehouse planning starts with analyzing key factors:
How many different stock keeping units (SKUs) are planned for storage?
What is the turnover frequency?
Are there seasonal fluctuations or special requirements?
What storage space and height are available?
What infrastructure is in place (floor, power, IT)?
How many pallets need to be moved per day?
These questions help define the right pallet storage system and an efficient warehousing strategy.
BENEFITS OF A PALLET WAREHOUSE.
- Maximum space utilization: Especially with high-bay warehouses and intelligent stacking strategies.
- Increased productivity: Through automation and optimized processes.
- Error reduction: Modern warehouse management systems minimize typical pallet storage errors.
- Cost savings: Efficient processes and energy savings reduce operational costs.
AUTOMATED PALLET WAREHOUSES: A GLIMPSE INTO THE FUTURE.
The future of pallet storage is clearly automated — offering companies enormous opportunities to increase efficiency, flexibility, and cost-effectiveness. With modern technologies such as innovative shuttle systems, robotics, and intelligent software solutions like our Fb Stash, warehouse processes can be significantly accelerated and precisely controlled.
Automated pallet warehouses not only enable maximum space utilization through compact, multi-level storage structures but also significantly reduce manual interventions. This leads to lower error rates and a decreased risk of transport damage. Additionally, real-time data and integrated warehouse management systems ensure transparent workflows, optimized inventory control, and rapid response times.
Another advantage is high scalability: automated systems can be flexibly adapted to changing storage requirements and growing product ranges without extensive renovations. Moreover, automated pallet warehouses score high on energy efficiency, as intelligent controls and demand-based usage minimize energy consumption.
For companies looking to grow or future-proof their logistics, automated pallet warehouses represent a decisive competitive advantage.
CONCLUSION: A GOOD PALLET WAREHOUSE REQUIRES FORESIGHT.
Whether block storage or shuttle system – a successful pallet warehouse is no coincidence. It’s the result of analysis, planning, experience and the drive to not just manage processes but improve them.
Depending on needs, a warehouse can be operated manually, semi-automatically or fully automatically. Always think ahead: How will the product range evolve? How flexible must the structure be? What expansions are realistic?
Those who plan their warehouse with foresight save time and costs in the short term – and lay the foundation for a powerful, scalable and future-proof logistics system.
FREQUENTLY ASKED QUESTIONS ABOUT PALLET WAREHOUSING.
A pallet warehouse is a specialized storage structure designed for the efficient storage and transport of goods on pallets or mesh boxes. It enables space-saving and organized storage, which is especially important in logistics and shipping operations.
There are several types of pallet storage systems, including:
-
Block storage: pallets are stacked directly on the floor, ideal for large quantities of the same item (LIFO principle).
-
High-bay racking: uses vertical space to store pallets on multiple levels, often with automated equipment.
-
Drive-in/drive-through racking: allows forklifts to enter the rack structure for deep storage.
The capacity of a pallet warehouse depends on factors such as the available space, the racking structure and the type of goods being stored. Precise planning that takes these elements into account is essential.
Common mistakes include:
-
Insufficient rack load capacity or incorrect stacking methods.
-
Failure to comply with safety regulations.
-
Lack of staff training.
-
Missing or inadequate warehouse management systems (WMS).
-
Maximum space utilization through efficient racking structures.
-
Increased productivity through optimized processes.
-
Reduction of errors and losses.
-
Cost reduction through automation and efficient warehouse management.
Efficient planning includes:
- Analysis of the types and quantities of goods.
- Selection of suitable racking and storage systems.
- Consideration of safety and ergonomic aspects.
- Integration of a warehouse management system (WMS).
- Regular training of warehouse staff.